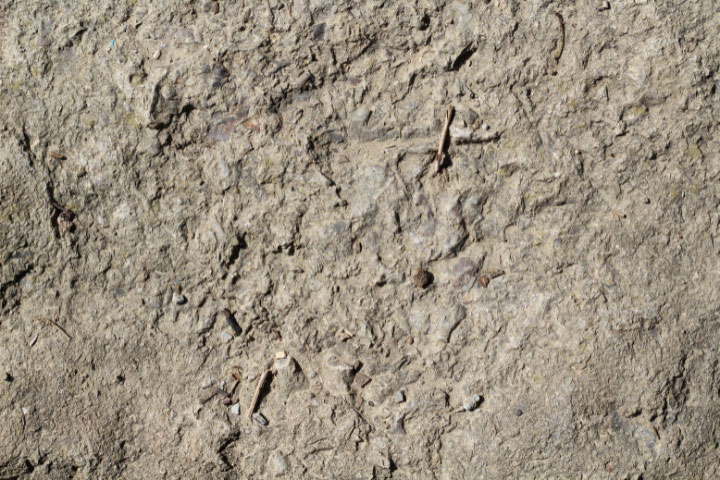
Now that we’ve looked into some of the problems you might run into when drilling through soft rock, let’s look at the other end of the scale. Anything over six on the Mohs scale of hardness is considered hard rock. This includes some often-encountered types such as silicified rock, quartz, chert, granite, and kimberlite.
One of the very first things that an experienced drilling company will do before making a game plan is to perform a hardness test of the site. This is a pretty simple test. You basically perform a scratch test on the ground using and etcher kit, and then compare it with the Mohs scale. This will give you a number which reflects the hardness of the ground, and it will help you select the right tools for the job.
Harder ground is generally seen as harder to drill through. However, one way to make it as easy as it can be is to choose the right bit. This is an important decision. Diamond drilling is required in order to penetrate hard rock. In order to drill through hard rock, you need a core bit with a higher number, one with a softer matrix and a free cutting edge. As the number designation of the bit gets higher, the diamonds encrusted in the matrix become more exposed, giving more cutting power to the bit. Both Hero 9 and Hero 11 are excellent bits for hard rock, and they both feature self-sharpening abilities as well.
The configuration of the bit face will also have an impact on its performance and penetration. For hard rock, One Pro tip from your favourite Sydney drilling company is to go for the turbo configuration when dealing with very hard rock. It has less surface area in contact with the rock, giving it a very free cutting bit. Plus, with the turbo configuration, the head is flushed and cooled while it’s in operation.
When drilling in hard rock, it’s crucial to keep a close eye on your parameters. Rotation speed, feed pressure, and water flow all need to be within tolerance. And the details are all important. Too little water flow will cause the bit to burn, but if you use too much, the blade won’t be able to sharpen.
Another area worth noting is the wear of the bit. Ideally, you want an even wear on the matrix and diamonds of the bit over the full depth of impregnation, rather than exposing the diamonds too far and risk them breaking off, or, on the other hand, polishing the bit face. Too low a rotation speed can overstrain the matrix, while too high a speed can ruin the bit by leaving the diamonds polished.
If you find that the drilling slows and then stops advancing, it’s possible that the bit has become polished, and that you need to sharpen it before it can be used again. Sharpening the bit is exposing the impregnated diamonds on the surface. This is a bit of an expert skill, and every bit is different, so you have to adjust your sharpening tactics to the individual bit.
If you have questions, feel free to contact us. At BG Drilling, we’ve got you covered.